Raw Materials for the Energy Transition
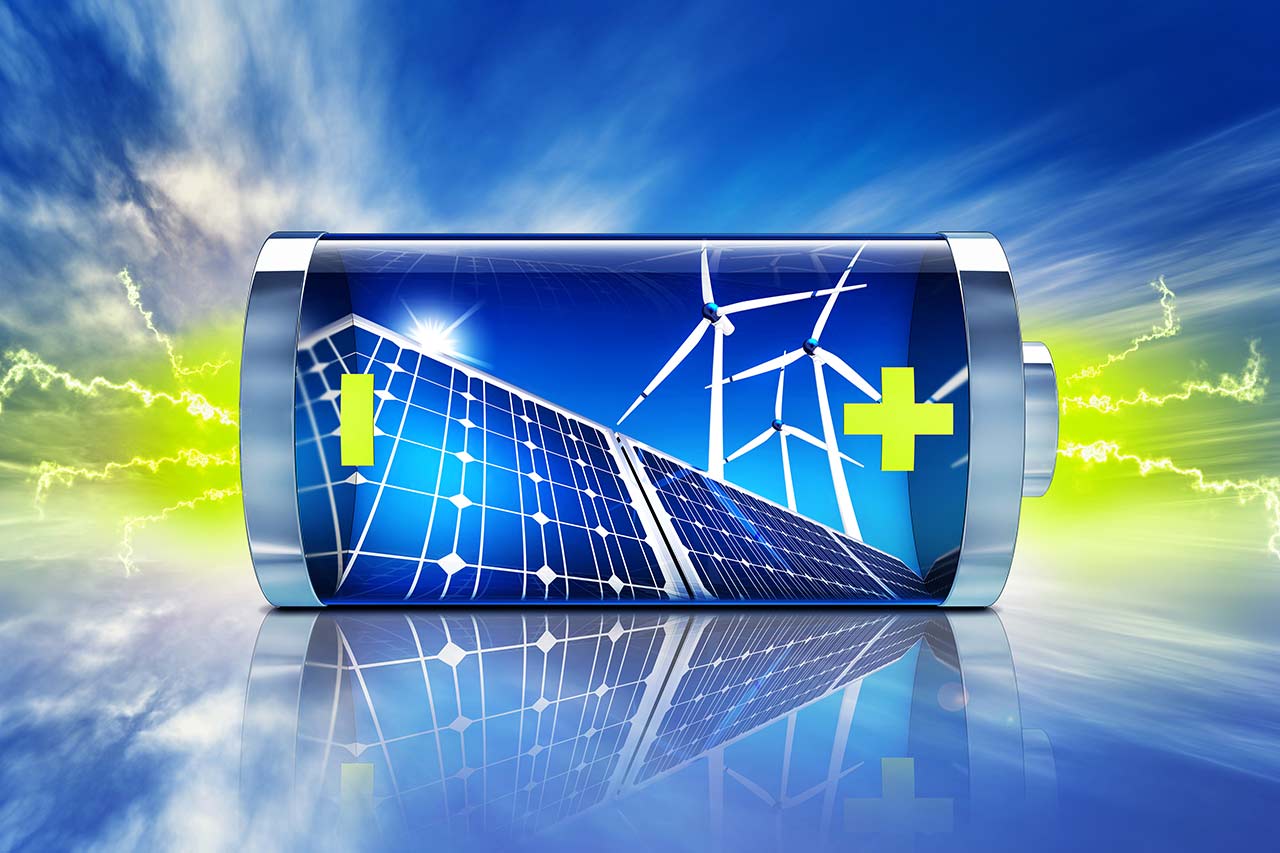
The Energy Transition requires raw materials present, in a quasi-monopolistic situation in some countries and whose reserves may be low, where recycling is difficult or is having a strong societal and environmental impact. ALCIMED, a consulting company in Innovation and New Businesses, examines the status of certain raw materials related to the Energy Transition, their applications and their major issues.
The Energy Transition is shaking up the global industry and is raising new raw material needs. Some of them are seeing their demand explode with the development of new technologies such as Li-ion batteries, photovoltaic panels or electric vehicles.
Based on data published by the European Commission, the Bureau of Geological and Mining Research (BRGM), the US Geological Survey or the British Geological Survey, ALCIMED examines certain raw materials that are critical to the Energy Transition.
The roll-out of electric vehicles and their autonomy are already at the heart of the debates because they are based on the development of Li-ion batteries…
Li-ion batteries are high consumers of raw materials such as lithium, cobalt, graphite, nickel, aluminium or copper as electrodes or electrolytes. Several forecasts indicate that the volume demand for these raw materials for batteries will increase by a factor of 38 by 2030 with the deployment of electric vehicles.
According to Bloomberg, lithium production will have to increase by 170%, cobalt by 74% and graphite by 41% by 2030 to satisfy world demand. The significant increase in demand for aluminium, manganese, aluminium and copper will have a smaller impact on the production of these raw materials (between 1 and 8%) since demand for other metallurgical or industrial applications will remain strong and significantly higher than that for batteries.
The secondary production sectors of copper, nickel, manganese and aluminium are well established, with, for example, a share of the world supply ensured by recycling 40, 32 and 25% respectively of nickel, copper and manganese. Secondary production of lithium and graphite is not very developed at the moment, probably because the reserves identified for these 2 minerals exceed 200 years.
China controls more than 68% of the world’s graphite production and Congo more than 60% of its cobalt production. Lithium production is shared between Chile and Australia with 75% of the world’s supply. The monopoly of certain countries is problematic and can impact the prices of certain materials. For example, Congo is considering imposing royalties on cobalt exports.
Many of these raw materials have strong environmental and societal impacts. For example, lithium mining causes soil and water pollution in the vicinity of mines. In addition, extraction requires significant quantities of water in sometimes arid areas such as northern Chile, leading to conflicts with local populations. Cobalt production today is characterised by child labour, significant dangers for miners (collapses, lung diseases, etc.) and pollution in the vicinity of mines. Finally, the extraction of graphite leads to major air pollution in China with high emissions of fine particles.
… and vehicle weight reduction.
Lighter vehicles are crucial to extend the batteries’ life. This is achieved by using alloys or superalloys containing high-risk raw materials such as chromium, rhenium, hafnium, tungsten, niobium, cerium or vanadium.
Niobium is an additive of choice in steels because it allows them to be lightened and their resistance to high temperatures to be increased. It is also used in the manufacture of pipelines and in the space industry. However, 90% of the production of this metal is controlled by Brazil, which could drive up prices if the country decides to limit its exports.
The photovoltaic industry is also reliant on certain critical raw materials.
Indium, cadmium, tungsten, tin, copper or silver are used to metallize cells or are used in the composition of panel semiconductors.
The sector is forecasted to grow by 40% per year! The markets for these raw materials are not very affected by this demand, which remains secondary compared to other needs, but the situation could change rapidly.
The Energy Transition is dependent on permanent magnets and China.
The neodymium-iron-boron alloy has exceptional magnetic properties enabling to significantly reduce the size of the magnets used in industry. These magnets are used in the manufacture of wind turbines, electric motors and electronic equipment.
Several rare earths such as praseodymium, neodymium, gadolinium or dysprosium are also included in the composition of these magnets. Despite the availability of these resources all over the world, more than 80% of rare earths are produced in China. In the early 2010’s, China had imposed quotas for its exports, which pushed prices up! The objective of this move was to force manufacturers to set up their magnet production plants in China through joint ventures, for example. As taxes do not apply to finished products, many manufacturers have shifted their know-how. Subsequently, these quotas were removed in order to lower prices and limit the creation of mining projects elsewhere in the world. Today China controls the production of raw materials and magnets.
The demand for magnets is exploding with the deployment of electric vehicles or wind turbines: a growth of 9% is expected each year over the next 5 years.
Nevertheless, the “image” of these magnets could be damaged in the future. Rare earth mining is very energy-intensive and their refining is very polluting. Each tonne of rare earth requires 200 m3 of water that will be contaminated with heavy metals and loaded with acid. These waters are released directly into the environment and are impacting populations near Baotou, the largest rare earth refining site: cancer rates are abnormally high and rice production has become impossible.
“The French and European Energy Transition is proving to be highly dependent on sensitive countries for its supply of raw materials. Among them, ALCIMED has identified neodymium, cobalt and praseodymium as critical. It is urgent for the industry to find substitutes, to strengthen recycling chains or to secure these supplies!” concludes Jean-Philippe Tridant Bel, Energy, Environment & Mobility Partner at ALCIMED.