4 key 3D printing trends impacting industries
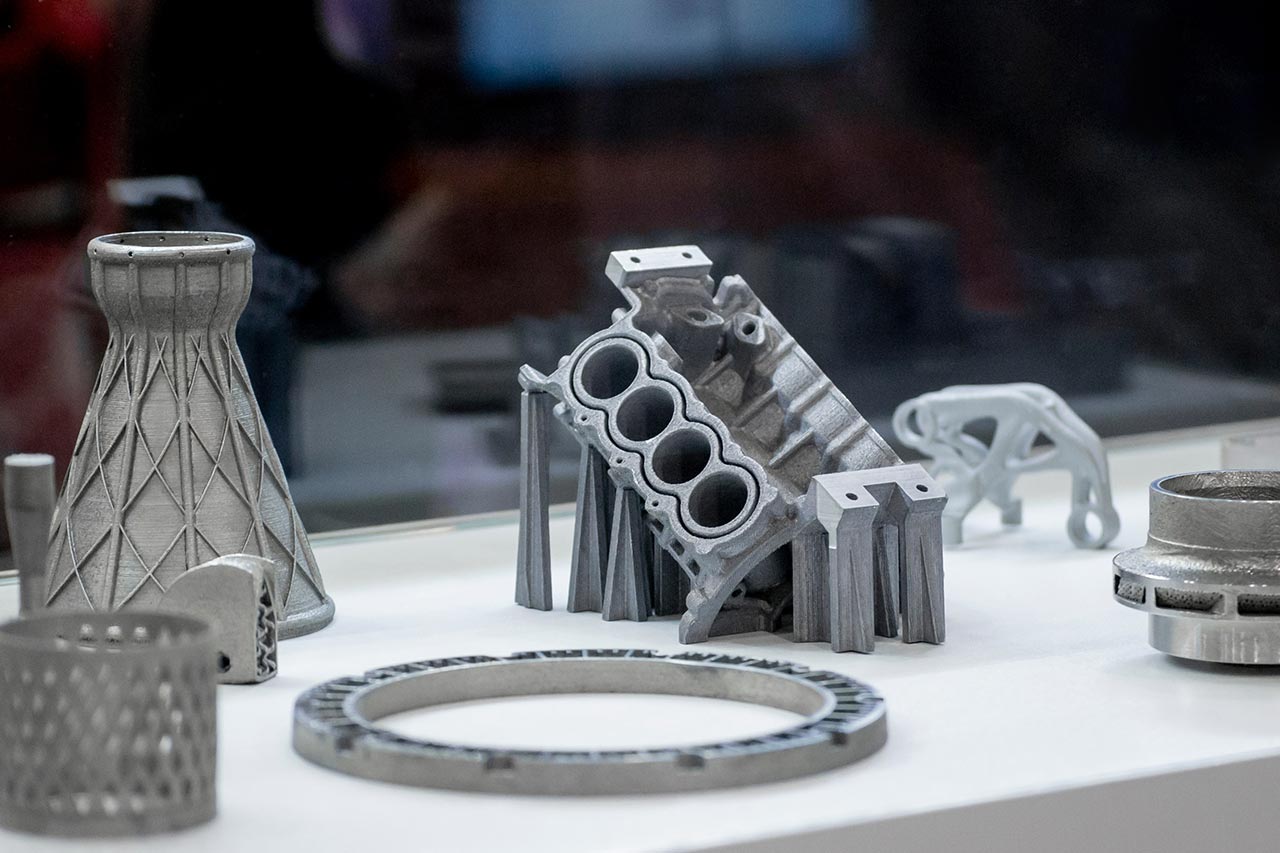
The expanding use of 3D printing is one of the main disruptive technologies at the heart of the Fourth Industrial Revolution. Also called “additive manufacturing”, this production process allows the manufacturing of a three-dimension element through a digital model and the successive addition of material layer by layer. 3D printing is increasingly used accross different industries, such as aerospace, automotive, healthcare, construction and energy industries. Alcimed identifies 4 important trends for the future of 3D printing.
1. New polymer materials are increasingly being used for 3D printing
Three types of materials are currently used for 3D printing: polymers (including plastics), metal and, more marginally, ceramics. These materials can be printed through several processes such as powder bed fusion processes, material jetting or material extrusion, among others.
Polymers are currently the most used material for 3D printing in industries. Most of them are standard materials as the traditional PLA and ABS that are simple and easy to process. However, PLA and ABS have reduced properties compared to more emerging technical thermoplastics such as PEI or PEEK. These thermoplastics are ideal for demanding engineering applications, for their high resistance to heat, chemicals and flames, their stiffness and thermal conductivity, especially in the aerospace, automotive and healthcare industries.
While polymer remains the most important segment today, the metal segment is growing at a fast pace. This segment comprises traditional materials such as stainless steel, titanium, aluminum, nickel and cobalt. But new metal “super-alloys” are also being developed, such as copper-titanium or Inconel (nickel-based advanced alloys). They are particularly interesting as they can increase the resistance of components and find useful applications for high-performance parts in the aerospace and healthcare industries.
2. More and more end-parts are being produced using 3D printing in industries
Applications in 3D printing are no longer restricted to prototyping as 3D printing is being increasingly used for tooling and industrial end-part production, thanks to new materials, more and more affordable 3D printers, and time reduction in the printing process: new printers can now print parts in minutes instead of hours a few years ago.
In the context of the Covid-19 global health crisis, many French automotive companies such as PSA, Renault, Faurecia and Michelin have been using 3D printing to hasten the production of respirators and masks. Before that, in the automotive industry, Volkswagen opened in 2018 a 3D Printing Center where tools and end parts’ larger batches such as cable mounts and switches are produced.
However, repeatability, accuracy and productivity remain important challenges to further development of 3D printing for end-part production. Some industrial players such as HP have been investing significantly to tackle these issues. The latter opened in June 2019 a 3D Printing and Digital Manufacturing Center of Excellence in Barcelona, where they partner with BASF or even Siemens to fasten innovation in this domain.
3. The value chain has been consolidating rapidly in industries
The 3D printing market has traditionally been segmented between 5 types of players, each being specialized on a segment of the value chain: manufacturers and suppliers of materials, OEMs (3D printers’ manufacturers), software providers, service providers and end users.
Two major integrated players, Stratasys and 3D Systems, are leading the market. But the ecosystem is very young, fragmented and in rapid evolution: big upstream and downstream players are extending their positions on the value chain through external acquisitions. For example, over the last four years, General Electric has developed a complete 3D printing offer through the acquisition of the materials supplier AP&C, the machine manufacturers Arcam & Concept Laser and the software provider Geonx. In 2019, the world leader in chemicals BASF acquired the French service provider Sculpteo to include more 3D printing services in its portfolio.
4. Generative design is a strong trend in conception services
Among services, players can propose rapid manufacturing (on-demand parts production), consulting services and conception services for design, inspection, scanning and printing.
Conception services stand out as key capabilities for 3D printing players to bring value to their clients. In this context, generative design is becoming a very strong trend that facilitates extension of customized and complex design expertise.
Generative design is a software-based iterative design process leveraging artificial intelligence. Unlike classic topology optimization, generative design does not focus on improving pre-existing design. It explores many alternatives based on design goals and constraint inputs, enabling time saving and increased precision to reach mechanical property targets.
In the automotive industry, General Motors, in collaboration with the software provider Autodesk, has produced in 2018 a generatively designed seat bracket that is lighter and stronger than a standard part. In the aerospace industry, Airbus is also exploring generative design possibilities to develop lighter–weight parts with better performance and safety standards.
The 3D printing sector is evolving: new materials are being used, more and more end-parts are being produced, the value chain is consolidating, and conception capabilities are evolving with generative design at the forefront. These strong trends will continue to transform industries such as aerospace, automotive, healthcare, construction and many more, offering several opportunities for players who want to innovate.
About the authors
Oussama, Consultant in Alcimed’s Energy Mobility & Chemicals team in France
Sylvain, Project Manager in Alcimed’s Energy Mobility & Chemicals team in France
Do you have an exploration project?
Our explorers are ready to discuss it with you