The digital transformation of production plants: a major future strategic challenge for the pharmaceutical industry
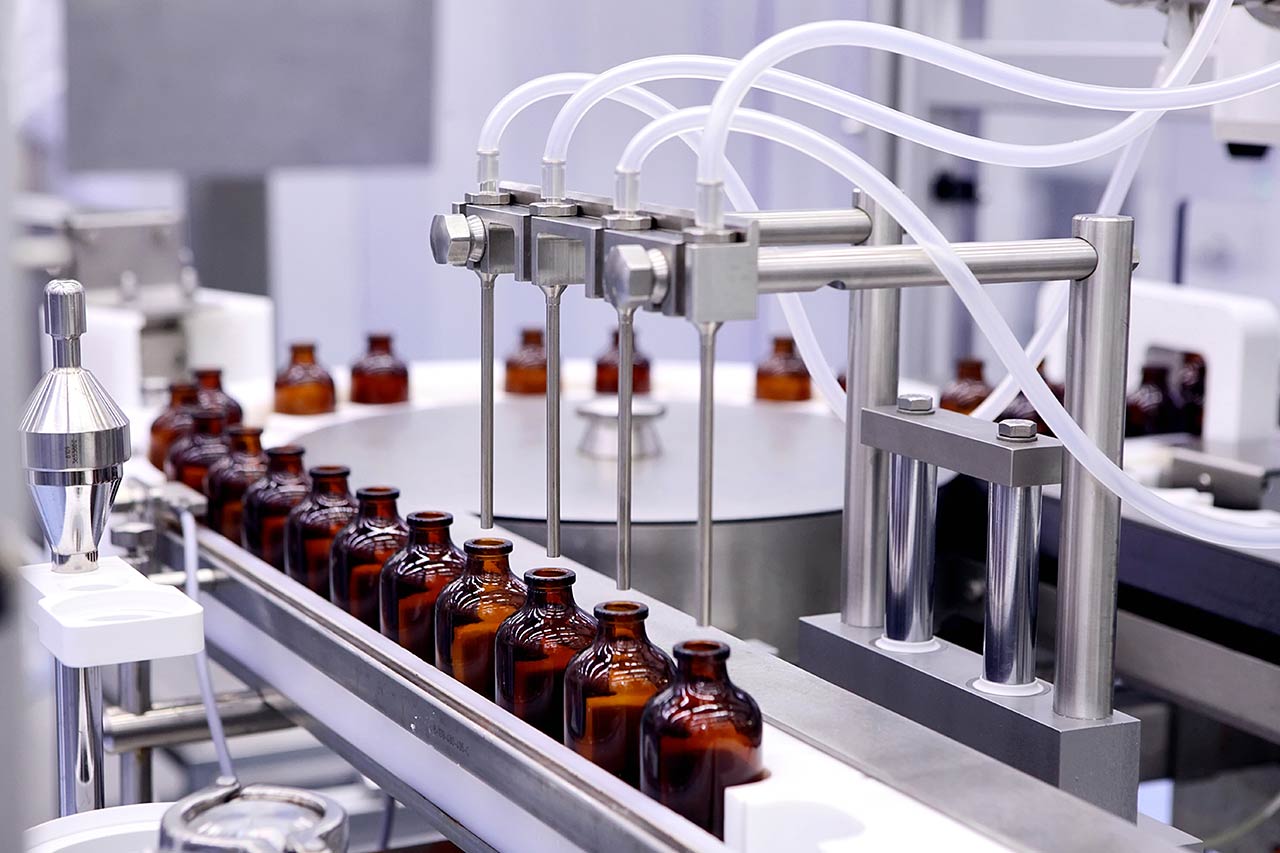
In a world marked by the growth of Industry 4.0, advanced digital technologies are now emerging in drug production chains and will become competitive and operational requirements to meet tomorrow’s health challenges. Alcimed, a consulting company specializing in innovation and the development of new markets, deciphers the challenges and opportunities offered by the digitalization of drug production lines and examines its prospects for pharmaceutical companies.
The digital revolution, already at work in many industrial sectors, is now beginning to gain momentum in the pharmaceutical sector. It is part of an emerging context of new ways of innovating and organizing production in increasingly connected, digitalized, robotized and intelligent factories. The introduction of disruptive digital technologies will revolutionize all activities along the entire value chain, from clinical development to pharmaceutical production and patient care. This fourth industrial revolution, better known as Industry 4.0, could be a possible response to the new challenges posed by the major trends that define the current health world. It would, for example, make it possible to cope with the growth of the global pharmaceutical market (+6% between 2016 and 2017), the rise of specialized drugs, produced in smaller volumes, or the emergence of personalized medicine and targeted therapies.
Learn more about the challenges of Industry 4.0 >
A digital transformation already initiated by certain pharmaceutical companies
Pharmaceutical companies are now using various levers to address these major challenges. In particular, breakthrough technologies, such as connected sensors, digital twins or augmented reality and virtual reality technologies, are major strategic development areas for pharmaceutical production models. Data collection and analysis, throughout the laboratory’s value chain, will be at the heart of the decision-making process and the continuous improvement of production activities.
The pharmaceutical group Sanofi is currently using, on a pilot scale, several artificial intelligence-based applications, such as the digital twin of its new Framingham unit. This exact 3D replica of the production plant makes it possible to deploy different employee training programs and to predict and optimize the manufacturing time of a drug, through numerical simulations and efficiency tests. Additionally, like Novartis[1] and Johnson & Johnson[2], Sanofi, through an investment of €60 million by the end of 2021[3], plans to equip certain production sites with connected equipment to deploy a strategy of operational excellence for its activities. The installation of connected equipment should make it possible to record several thousand parameters throughout the drug manufacturing process to generate data to control, analyze and supervise production. Analytical techniques can then be used to detect any operating deviations. The drug production circuit can, therefore, be monitored in real-time and the rise of artificial intelligence algorithms suggests the possibility of setting up predictive maintenance programs, aimed at anticipating drops in the performance of production machines, preventing machine downtime and thus reducing supply disruptions.
Other manufacturers, such as GlaxoSmithKline[4], rely on the use of augmented and virtual reality tools to store and display documentation and instructions for operators to reduce the use of paper and facilitate information sharing between the various stakeholders. Recent technological advances have made it possible to disseminate these immersive technologies more widely, developing human-machine interactions, while ensuring the convergence of the virtual world with real tools and products.
This transformation opens up a wide range of opportunities for the pharmaceutical sector
“This progressive digitalization of industries is intended to make them more flexible, reliable, efficient and competitive,” says Céline Leroy, a consultant at Alcimed. Increased control of manufacturing processes will make it possible to obtain reproducible and more reliable results for patients, particularly in the production of biotechnological drugs[5]. In this context, as part of its Critical Path Initiative (CPI), the FDA encourages the use of “Process Analytical Technologies” to ensure the quality and efficiency of drug production. In 2008, the American agency initiated an exploration of the potential of these analytical technologies in the production of biomedicines (such as monoclonal antibodies or recombinant proteins)[6], emphasizing the need to modernize the production techniques of pharmaceutical manufacturers.
In addition, continuous monitoring of operations without interrupting production activities will, for example, reduce unplanned machine downtime by 30% to 40%[7]. Thus, at the end of this digital transition, the reduction in maintenance costs and the adaptability of the production model make it possible to envisage a potential gain of 1 to 2 billion euros for the French pharmaceutical sector[8]. The gradual digitization of factories could ultimately increase the production efficiency of innovative medicines and allow dosage to be adapted to patient profiles, thus creating a digital, patient-centered ecosystem8.
Many challenges remain to be met before the digitalization of production chains on a larger scale
Nevertheless, several obstacles related to the implementation and appropriation of these breakthrough technologies still hinder their deployment on a larger scale.
Firstly, it seems essential for the various players in the pharmaceutical sector to acquire the skills to analyze information and master these cutting-edge technologies, internally or through partnerships. Secondly, the training and support of employees in this transformation within the company will be essential to encourage team commitment. Finally, the integration of these new technologies into the company’s activities, the storage, and protection of collected data are also key challenges facing manufacturers wishing to embark on this digital revolution.
“The digital transformation of production plants will revolutionize the practices of many pharmaceutical companies,” says Lambert Lacoste, Alcimed’s project manager. “It will enable the players in the sector to rethink their entire healthcare offer. The digitization of the industrial network is the first step towards the automation of production lines and personalized medicine; the potential answers to the major health challenges of our century”.
[1] Novartis, Go big on data and digital – Annual Review (2018)
[2] Johnson & Johnson, 3 ways Johnson & Johnson is harnessing digital innovation to better deliver medicine to you (2018)
[3] Sanofi, La révolution digitale – Usine digitale 4.0 (2018)
[4] GSK, The digitalisation lab : bringing the digital age to manufacturing (2016)
[5] Amgen, La production des biomédicaments : un savoir-faire industriel de haut niveau (2019), www.amgen.fr/science/defis-production-medicaments/
[6] Food & Drug Administration, The critical path initiative – Report on Key Achievements in 2009 (2009)
[7] Augustin Marty, L’Intelligence Artificielle : la solution à la productivité des entreprises pharmaceutiques, L’Usine Nouvelle (2018)
[8] Sanofi, L’usine du futur (2018), www.sanofi.com/fr/science-et-innovation/l-usine-du-futur
Do you have an exploration project?
Our explorers are ready to discuss it with you