Des voitures en plastique, la réalité de demain ?
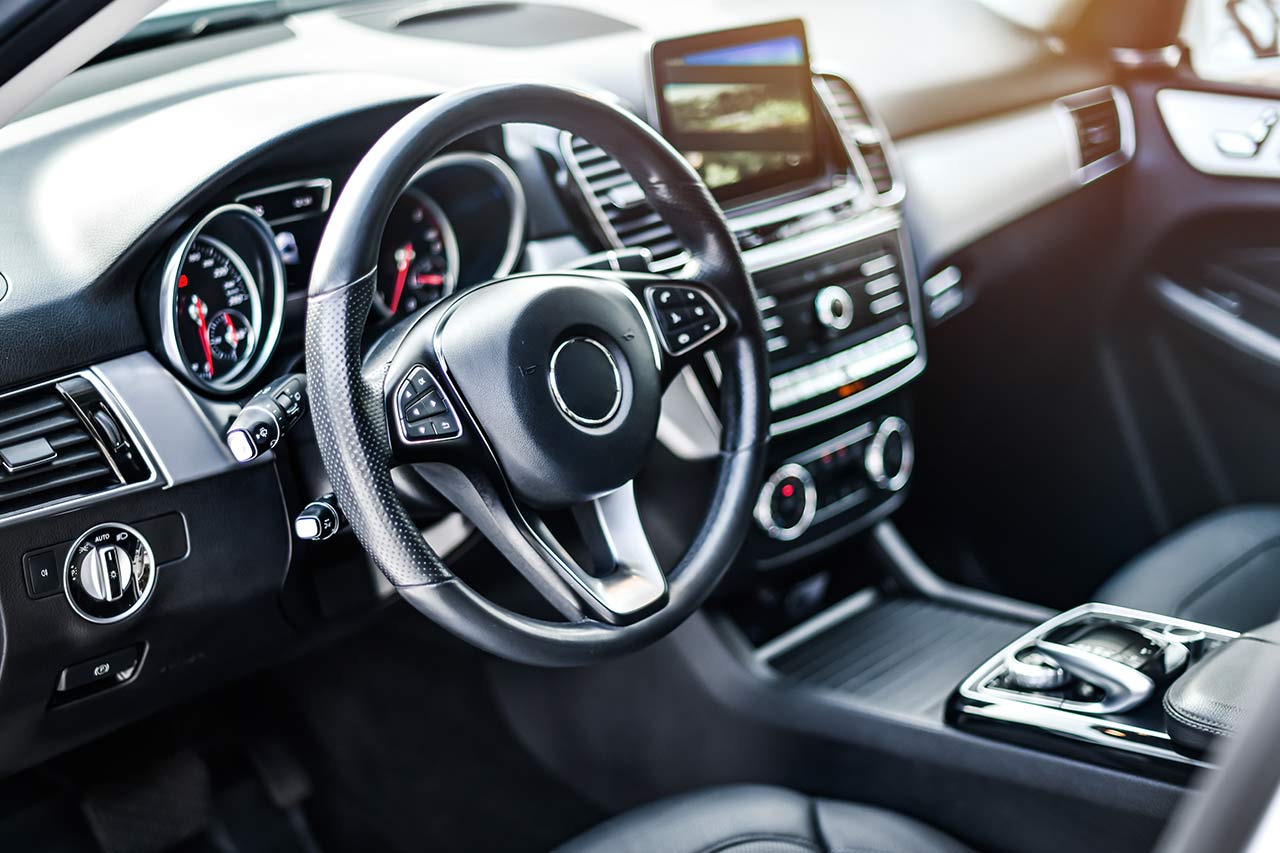
Avec des objectifs de réduction des émissions de CO2 toujours plus bas imposés par l’Union Européenne, les constructeurs doivent s’adapter. La première solution possible est l’électrification du parc automobile. La seconde est l’allégement des véhicules thermiques pour réduire leurs émissions. Substituer les pièces métalliques par des pièces plastiques ou composites pourrait permettre des gains de poids substantiels. Au regard de leurs propriétés, ces matériaux atteignent le niveau de performances des métaux, mais alors pourquoi nos véhicules sont-ils encore majoritairement constitués de métal ? ALCIMED, société de conseil en Innovation et Développement de Nouveaux Marchés, dresse un bilan sur l’utilisation des matériaux plastiques dans l’industrie automobile et sur les freins à leur démocratisation.
L’Union Européenne a fixé aux constructeurs automobiles européens un objectif de 95 grammes de CO2 maximum émis par kilomètres parcourus d’ici 2021 (valeur moyenne valable pour un véhicule de 1390 kilogrammes, soit le poids moyen des nouveaux véhicules mis sur le marché). Mi-décembre 2018, le Parlement et le Conseil Européen sont arrivés à un consensus en fixant un nouvel objectif de diminution des émissions moyennes de CO2 de 15% d’ici 2025 et de 37,5% d’ici 2030 par rapport aux résultats obtenus en 2021. La situation reste cependant très disparate entre les constructeurs comme le souligne le dernier rapport de l’ICCT (International Council on Clean Transportation). Alors que Toyota est le constructeur le plus proche de sa cible pour 2021 (avec une diminution de 9 grammes supplémentaires restant à atteindre), d’autres ont encore d’importants efforts à fournir. Des constructeurs comme Fiat, Chrysler, Hyundai, Ford, Volkswagen ou Daimler, sont encore à plus de 25 grammes de leurs objectifs pour 2021, ce qui paraît de plus en plus difficile à réaliser.
Une feuille de route pour la réduction des émissions de CO2
L’électrification du parc automobile reste une solution, cependant le faible taux de pénétration des véhicules électriques ne permettra pas aux constructeurs d’atteindre leur cible de 2030. En effet, il est prévu que 75% des véhicules vendus cette même année soit toujours des véhicules essence ou gasoil. Les constructeurs ont toutefois plusieurs leviers pour atteindre l’objectif de baisse d’émissions. Le plus efficace serait de travailler sur les motorisations, par exemple en diminuant les cylindrées. Cependant plusieurs experts s’accordent à dire qu’un plateau de performances serait atteint. Le second levier est l’allègement des véhicules, et la substitution des pièces métalliques par des matières plastiques semble être une solution prometteuse.
Un véhicule composé de plus en plus de matières plastiques
Le marché des plastiques dans le secteur automobile est estimé à quelques 25 milliards d’euros en 2016 pour 10 millions de tonnes. Il est prévu que sa croissance d’ici à 2025 soit d’environ 10% par an. Cette évolution n’est pas seulement portée par l’augmentation des ventes de véhicules, estimée à 2% chaque année ; elle est également la conséquence de l’intégration des matières plastiques dans de nombreuses applications jusqu’à maintenant réservées au métal.
Aujourd’hui encore, 80 % du poids des véhicules concerne des pièces métalliques. Certains experts estiment que l’utilisation des plastiques pour la structure du véhicule permettrait des gains de poids substantiels, allant jusqu’à plus de 200 kilogrammes et correspondant à une diminution des émissions de CO2 d’environ 12 grammes.
A l’heure actuelle, 50 % du plastique utilisé dans les véhicules l’est pour des éléments de carrosserie. Il s’agit principalement de PP (polypropylène) présent dans les capots, les hayons, les parechocs, les ailes… Le deuxième poste d’utilisation majeure des matériaux plastiques concerne l’intérieur des véhicules (40%), notamment les planches de bord ou l’intérieur des portes. Il s’agit alors principalement de PP, de PU (polyuréthane) ou d’ABS (acrylonitrile butadiène styrène). Enfin, des plastiques de spécialité, comme le PPS (polysulfure de phénylène), le PEEK (polyétheréthercétone) ou le PA (polyamide), sont également utilisés pour des applications dans l’environnement moteur. En effet, des propriétés spécifiques (chimiques, thermiques, etc.) sont nécessaires pour les systèmes de ventilation, de distribution du carburant ou les réservoirs. Ces derniers sont un parfait exemple de pièces dont la composition a entièrement basculé du métal vers le plastique.
PSA a récemment intégré des matériaux composites dans sa plateforme modulaire EMP2 à destination d’une quinzaine de véhicules de sa gamme. Un nouveau plancher arrière en thermodurcissables renforcés avec des fibres de verre a notamment été développé avec Plastic Omnium pour la 308. Pour toutes ces pièces structurelles ou semi-structurelles, les matériaux plastiques utilisés sont renforcés avec des fibres de verre, de carbone ou naturelles. Ces fibres sont requises pour obtenir des matériaux avec des propriétés physiques, notamment en rupture sous contrainte, suffisantes pour passer les crash-tests.
Des freins majeurs à la démocratisation et à une transition rapide
Malgré des propriétés mécaniques qui atteignent les niveaux de performances des matériaux métalliques, les matériaux composites tardent à s’imposer largement sur ce secteur. Les freins identifiés sont principalement les coûts mais également la sécurité et le recyclage :
- – Coût élevé de la production. L’outil industriel de l’industrie automobile est conçu pour la production de pièces métalliques. Les investissements requis pour changer les lignes de production seraient colossaux. De plus, les cadences de l’industrie automobile sont impressionnantes, et seraient impossibles à tenir avec les matériaux composites. Il faudra donc profiter d’un changement de plateforme modulaire pour réaliser les investissements requis et favoriser l’intégration des matériaux composites dans les véhicules.
- – Coût élevé des matériaux. L’industrie automobile doit maintenir des coûts bas. L’acier ou l’aluminium coûtent entre 1 et 3 €/kg. Les fibres de carbone reviennent à environ 15€/kg. Des projets comme FORCE II (IRT Jules Verne) visent à diminuer le coût de ces fibres et à le faire passer sous la barre des 8€/kg.
- – Incertitude quant à la prédiction des comportements durant les crashs. Alors que le comportement des aciers sous contraintes est parfaitement connu et donc prédictible, celui des matériaux composites est moins reproductible. Il est plus difficile pour les constructeurs de prévoir le comportement de ces matériaux durant les crashs et d’assurer la sécurité des passagers.
- – Complexité du recyclage. La réglementation en vigueur impose que 85% des matériaux de chaque véhicule soient recyclables. L’acier est très bien recyclé, ce qui n’est pas le cas des matériaux composites.
Quels sont les leviers ?
La démocratisation des matières plastiques, et spécifiquement des matériaux composites, dans le secteur automobile sera donc forcément liée au développement de nouvelles familles de matériaux moins chers ou issus de process de fabrication plus simples, permettant notamment de hautes cadences.
Les producteurs ont adopté différentes stratégies pour diminuer les coûts. Certains travaillent sur le design des pièces ou sur la facilité de leur intégration. On peut par exemple s’intéresser au cas du plancher de la Peugeot 308 qui, autrefois composé de 30 pièces métalliques, est passé à seulement 4 pièces, en plastique cette fois. Cette modification a permis de diminuer le nombre de manipulations sur les lignes et donc de réduire le coût final. Un cadre métallique a, de plus, été ajouté à la pièce pour faciliter son intégration dans le véhicule.
Si un remplacement intégral du métal par du plastique n’est pas pour demain, certains constructeurs ont tout de même entamé cette révolution. Par exemple la start-up Gazelle Tech ou BMW proposent des véhicules disposant d’un cockpit intégralement constitué de matériaux composites.
« Certains constructeurs ont une stratégie ambitieuse comme BMW avec sa i3. Il s’agit d’un tournant et d’un exemple pour les autres constructeurs qui observent attentivement l’évolution de ces matériaux dans le temps. Le prix de ce véhicule reste encore trop élevé pour que l’on puisse parler de démocratisation. » conclut Jakub Rams, Manager de l’équipe Energie, Environnement & Mobilité chez Alcimed.
Vous avez un projet d’exploration ?
Nos explorateurs sont prêts à en discuter avec vous